Planetary Micro Mill PULVERISETTE 7 premium line ...
FRITSCH Planetary Ball Mills – high-performance all-rounder in routine laboratory work . The Planetary Micro Mill PULVERISETTE 7 premium line with 2 grinding stations is designed for a broad range of applications and ideally suited for loss-free grinding down to a final fineness of 100 nm of hard, medium-hard and brittle materials. Depending on the desired final fineness, the …
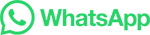