AVAILABLE AND EMERGING TECHNOLOGIES FOR …
material is separated in a classifier that is re-circulated and returned to the mill for additional grinding to ensure a uniform surface area of the final product. (Coito et al., 2005, and others.) Figure 1 presents a diagram of the cement manufacturing process using a rotary kiln and cyclone preheater configuration.
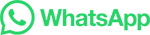