Optimisation in the US | World Cement
Additionally, the ball mills and the vertical raw mill reached 4 – 5% improvement on specific energy consumption. At the kiln, the savings of specific thermal energy consumption totalled 3.4%. All five assets are maintained and currently used in closed-loop mode without human intervention, while the process is in a steady state.
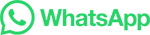