WEAR SOLUTIONS
H-E Parts provides a full range of wear management products covering the world's largest gyratory crushers, SAG and ball mills, jaw crushers, cone crushers, wear materials and associated lifting devices. Complementing our internal manufacturing capabilities, our supply network consists of some of the best manufacturers in
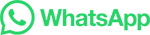