Grinding Process In Industries - Henan Mining Machinery ...
grinding process in cement industry. Jul 17, 2012 - Gulin crushing, screening, grinding and washing plant play a great role in aggregate production, ore processing ... ATLANTIC Bar grinding Bar grinding is especially used in the steel industry. There are two different grinding processes. process grinding surface
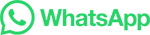