Used Vibro Energy Mills for sale. Sweco equipment & more ...
Sweco DM-4L Vibro Energy Mill. Manufacturer: Sweco Used Sweco Vibro Energy grinding mill, model DM-4L, high amplitude design, approx. 4 cu ft capacity, ply elastomer lined, on base with 2.5 hp, 230/460 volt motor, serial# 69973-A694. Sweco DM-4L Vibro Energy Mill
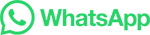