4.1 Introduction 4.2 Types of grinding machines 4.2.1 ...
cutting edges. The machine on which grinding the operation is performed is called a grinding machine. Grinding is done to obtain very high dimensional accuracy and better appearance. The accuracy of grinding process is 0.000025mm. The amount of material removed from the work is very less. 4.2 Types of grinding machines
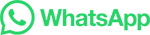