Simulation of a Laboratory Scale Ball Mill via Discrete ...
The simulations of dry mill were conducted by using a standard coefficient of restitution of 0.3 and a friction coefficient of 0.75 (ball-ball and ball-liner collisions) [ 20 ]. The charge consisted of powders and balls with filling of 40% of the charge (by volume). The specific gravity of the media is …
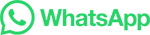