Custom Chemical Grinding & Milling Services | Seatex
Grinding and milling services by Seatex deliver standardized particle sizes for your products, every time. Ensuring particles are tightly grouped into a narrow distribution enhances a product's flow properties, as well as its ability to disperse and dissolve in water or other liquids.
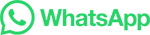