Grinding Manufacturing Process Engineer Jobs, Employment ...
582 Grinding Manufacturing Process Engineer jobs available on Indeed. Apply to Process Engineer, Manufacturing Engineer, Senior Process Engineer and more!
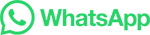
582 Grinding Manufacturing Process Engineer jobs available on Indeed. Apply to Process Engineer, Manufacturing Engineer, Senior Process Engineer and more!
Manufacturing grinding balls, there are four essential steps. First melting, second molding, third separating, and the last heat treatment. Melting. The furnace the factories most used are the medium frequency induction furnace, fast and stable. It's easy to add the ferrochrome and the other elements inside.
The process described above is the most general, and typical, manufacturing process that a small optic goes through. There are a variety of other manufacturing methods that are used for large optics, aspheres, plastics, and …
5 Facts About Grinding Processes. Grinding is machining process that's used to remove material from a workpiece via a grinding wheel. As the grinding wheel turns, it cuts material off the workpiece while creating a …
POINTING & GRINDING. We specialize in high volume manufacturing of precision stainless steel medical and surgical needles with multifaceted and taper points. Medical Needle Manufacturing Services. Use our experience in needle manufacturing and process equipment design, development and building
Manufacturing Process: Grinding. Grinding, also called surface grinding, is a machining operation in which material is removed using a powered abrasive wheel, stone, belt, paste, sheet, compound, etc. to realize fine finish tolerances and surface finishes. While there are a number of ways to grind parts, grinding is a more precise method of ...
Manufacturing Process. Quarry. Step 1: Quarry. ... Step 2 : Proportioning Blending & Raw Grinding. The raw materials are analyzed in real-time using cross-belt analyzers and in the plant laboratory, blended in the proper proportion, and then ground even finer. Plants grind the raw materials with heavy, wheel-type rollers that crush the ...
Manufacturing process of grinding is used to better the quality of the surface of the material. Normally is used as a finishing process in the end of the man...
Two enabling technologies -- superabrasive wheels and high precision servo control -- come together to provide a contour grinding process that resembles an OD turning operation. For many medium volume OD grinding applications, this method may be a means to consolidate several manufacturing steps into a single setup.
The Manufacturing Process Most grinding wheels are manufactured by the cold-press method, in which a mixture of components is pressed into shape at room temperature. The details of processes vary considerably depending upon the type …
Back End(BE) Process Wafer Back Grinding • The typical wafer supplied from 'wafer fab' is 600 to 750μm thick. • Wafer thinned down to the required thickness, 50um to 75um, by abrasive grinding wheel. › 1st step : Use a large grit to coarsely grind the wafer and remove the bulk of the excess wafer thickness.
One significant benefit to grinding is the compressive residual stresses that are imparted into the surface of the part during a machining process. If residual stresses are causing parts to twist, warp or bend after your machining …
The invention discloses a grinding wheel manufacturing method which comprises the following steps of material mixing, wherein quantified grinding materials and binding agents are mixed and prepared according to a technical formula; extrusion forming, wherein the prepared mixed materials are added in a die cavity to be extruded and formed; curing and sintering, wherein a …
The grinding wheel or the regulating wheel or both require to be correctly profiled to get the required taper on the workpiece. 29.2.5 Tool post grinder A self powered grinding wheel is mounted on the tool post or compound rest to provide the grinding action in a lathe. Rotation to the workpiece is provided by the lathe spindle.
slag grinding process diagram . slag cement flow diagram process slag cement flow diagram process Get the price As one of leaders of global crushing and grinding industry manufacturing process slag grinding unit 600 000 t/a slag grinding line with Production Process The stacked slag is packed and feed Below is the structure of the vertical ...
The invention discloses a process for manufacturing a high precise electroplating CBN (Cubic Boron Nitride) grinding wheel, comprising the following steps of: preparing a substrate and abrasive particles; preparing a plating solution; placing sand and electroplating; carrying out contouring improvement treatment on the abrasive particles; and carrying out the post-plating …
Belt grinding has become an important production process, in some cases replacing conventional grinding operations such as the grinding of camshafts. Belt speeds are usually in the range of 2,500 to 6,000 ft/min. Machines for abrasive-belt operations require proper belt support and rigid construction to minimize vibration.
The manufacturing process for grinding wheels begins with the selection of raw materials. The next step is mixing the raw materials and calibration of the proportions of each needed. This is ...
Machining is a term used to describe a variety of material removal processes in which a cutting tool removes unwanted material from a workpiece to produce the desired shape. The workpiece is typically cut from a larger piece of stock, which is available in a variety of standard shapes, such as flat sheets, solid bars, hollow tubes, and shaped beams.
Manufacturing process of grinding is used to better the quality of the surface of the material. Normally is used as a finishing process in the end of the man...
Grinding Fine finishes and precise dimensions perfect your product. And our CNC 7-axis grinding machines can custom form rasps, drills, taps, and reamers out of almost any material to your exact specifications. We have also perfected custom-profile grinding of complex shapes, including knee implants, custom implants, trials and forms.
The process involves the following stages: 1. Incoming inspection of preform. For the production of grinding balls, Energosteel uses hot rolled round bar from medium and high carbon and low-alloyed steel produced by the world's leading metallurgical companies. Prior to the production, the preform is subjected to strict control against the ...
Grinding process control balances these three interactions to achieve the desired parameters. These interactions feed into three major commercial grinding processes: rough grinding, precision grinding and ultra …
The process optimized end-of-arm package solution Active Angular Kit compensates tolerances on workpieces and applies a consistent contact force. That way the AAK delivers exactly reproducible deburring quality even on complex shaped objects. Industrial grinding and deburring processes can be automated and optimized for 24/7 production.
Grinding is a subset of cutting, as grinding is a true metal-cutting process. Each grain of abrasive functions as a microscopic single-point cutting edge (although of high negative rake angle ), and shears a tiny chip that is analogous to what would conventionally be called a "cut" chip (turning, milling, drilling, tapping, etc.).
Its primary function is in the realm of grinding holes for drill bushings and grinding pins. It can also be used for complex surface grinding to finish work started on a mill. Gear grinder, which is usually employed as the final machining process when manufacturing a high-precision gear. The primary function of these machines is to remove the ...
Manufacturing grinding balls, there are four essential steps. First melting, second molding, third separating, and the last heat treatment. Melting. The furnace the factories most used are the medium frequency induction furnace, fast and stable. It's easy to add the ferrochrome and the other elements inside. The raw material we required is ...
grinding machines, bufting machines. and reciprocating surface grinding machines. UTILITY GRINDING MACHINES The utility grinding machine is intended for offhand grinding where the workpiece is supported in the hand and brought to bear against the rotating grinding abrasive wheel. The accuracy of this type of grinding machine depends on the
The centerless grinding process is one where a set of rotary wheels are used to remove material from an object or work piece. The process is preferred for manufacturing where a large number of work pieces must be handled and processed in a...
manufacturing, and coated abrasive product manufacturing. Abrasive grain manufacturers produce materials for use by the other abrasives manufacturers to make abrasive products. Bonded abrasives manufacturing is very diversified and includes the production of grinding stones and wheels, cutoff saws for masonry and metals, and other products.
حقوق النشر © 2024.Artom كل الحقوق محفوظة.خريطة الموقع