FLOTATION PLANT DESIGN AND PRODUCTION PLANNING …
mill optimisation is a solid understanding of the resource to be processed. ... and the an ore sampling program and subsequent laboratory testing of these samples in order to extract process model parameters, • geostatistical distribution throughout the resource model of the process parameters, • mill and by the manner in which the ...
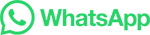