A SUMMARY OF TECHNICAL EVALUATIONS ... - EMC Cement
concrete, all enhancing the sustainability of construction and reducing the cost of ... low-energy process consisting of mechanical grinding and ac tivation. The end-product has a high degree of amorphization, optimized particle-size distribution and improved surface ... The proportion added to concrete so as to
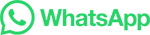