Spot Prices of Imported Iron Ore Continued to Rise amid ...
SHANGHAI, Dec 6 (SMM) – The production resumption at many steel mills have pushed the iron ore spot and futures prices higher last week. For the spot prices at ports, mainstream PB fines in Shandong saw a weekly gain of 40-50 yuan/mt and the prices stood at 685 yuan/mt. Taking into account that Tangshan city has issued another notice of stricter …
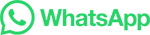