Ball milling: An experimental support to the energy ...
@article{osti_186764, title = {Ball milling: An experimental support to the energy transfer evaluated by the collision model}, author = {Magini, M and Iasonna, A and Padella, F}, abstractNote = {In recent years several attempts have been made in order to understand the fundamentals of the ball milling process. The aim of these approaches is to …
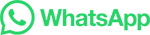