Problem 2 [8 marks] You have sampled the discharge | Chegg
Problem 2 [8 marks] You have sampled the discharge stream of a grinding mill and you would like to determine if the mill is operating properly. Through mineralogical analysis, you determine that the target grind size for good mineral liberation is an 80% passing size of 212 um. You perform a screen analysis of the mill discharge stream; the ...
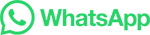