Modernization of a Tandem Cold Rolling Mill at …
n-stand rolling mills. The model was used to simulate the plant in respect of the normal rolling mill practice, for the strip threading and tailing-out as well as the dynamic pro-gram change (DPC) for the technological functions such as reference generation, drives, roll gap posi-tioning and thickness and tension control.
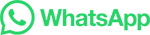