Grinding Mills and Their Types – IspatGuru
Rotational speed is usually fairly low, about 80 % of critical speed (critical speed is the speed at which the charge will be pinned to the rotating drum and does not drop) and typical drum diameter ranges from 2 to 10 meters. This type of mill is often used as a single stage process, providing sufficient size reduction in a single process ...
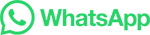