ball mill sizing calculation spredsheet
How to Size a Ball Mill Design Calculator Formula A) Total Apparent Volumetric Charge Filling – including balls and excess slurry on top of the ball charge, +86 21 …
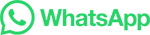
How to Size a Ball Mill Design Calculator Formula A) Total Apparent Volumetric Charge Filling – including balls and excess slurry on top of the ball charge, +86 21 …
CYCL and MILL models were selected to simulate SAG mill, Hydrocyclone packages and ball mill units. SAGT and MILL models both are based on the population balance model of grinding process. CYCL model is based on Plitt's empirical model of classification process in hydrocyclone units. It was shown that P
Ball Mill Power Calculation Example #1. A wet grinding ball mill in closed circuit is to be fed 100 TPH of a material with a work index of 15 and a size distribution of 80% passing ¼ inch (6350 microns). The required product size distribution is to be 80% passing 100 mesh (149 microns). In order to determine the power requirement, the steps ...
The present invention is directed toward a material handling, processing and milling facility which utilizes ball milling as a means for material grinding, mixing or mechanical alloying of materials. The system includes an automatic ball charging, agitating and indexing assembly, constructed and arranged to deagglomerate and directly distribute a plurality of grinding balls to the facility.
method is more efficient in achieving fine particle size. Rod mills: Horizontal rods are used instead of balls to grind. Granularity of the discharge material is 40-10 mm. The mill speed varies from 12 to 30 rpm. Planetary mill: High energy mill widely used for producing metal, alloy, and composite powders. Fluid energy grinding or Jet milling:
This project is to design and fabricate the mini ball mill that can grind the solid state of various type of materials into nano-powder. The cylindrical jar is used as a mill that would rotate the material that about to be ground, a motor is used to power the system so that the jar can rotate in high speed and using the regulator controls the speed of the rotation of the jar.
Ball mill is typically used to grind and/or blend materials and it can be done wet or dry. It can be used to mix ceramic powders, disperse particles in solvents, homogenize ceramic slurries, etc. Ball mills operate by rotating plastic jars around a horizontal axis, partially filled with the material to be ground plus the grinding medium.
torque mill test is the mill energy input divided by the solids load. The energy specific cumulative grinding rate at each screen size is calculated from a torque-mill test as in the example that follows. Torque mill solids load during test: 11.25 kg (24.8 lb) of ball mill feed sample from plant survey. Sample is reconstituted with water to be
Inventor Cam, breaking edge with ball mill. I need to break an edge along a compound angles, basically along 2 chamfers intersect using a 1/8 ball mill. I have tried using trace, it follows the path in simulation but not with posted g-code, in the passes tab I use sideways compensation "left" but it does not add a G41 cutter comp, I attached ...
Principle of Ball Mill : Ball Mill Diagram. • The balls occupy about 30 to 50 percent of the volume of the mill. The diameter of ball used is/lies in between 12 mm and 125 mm. The optimum diameter is approximately proportional to the square root of the size of the feed. The shell is rotated at low speed through a drive gear (60-100 rpm) and ...
Ball milling is a size reduction technique that uses media in a rotating cylindrical chamber to mill materials to a fine powder. As the chamber rotates, the media is lifted up on the rising side and then cascades down from near the top of the chamber. With this motion, the particles in between the media and chamber walls are reduced in size by ...
For overflow ball mills, the charge should not exceed 45% of the mill volume . For grate discharge mills, the charge should occupy about 50% of the mill volume . Bond developed a relationship that can be used to determine the percent charge by volume as a function of the vertical height above the charge, He, and the radius of the mill, R, i.e.,
Spreadsheet that accompanies the Procemin 2016 paper by Alex Doll. ... A simple method of assessing ball mill health using bond tests and functional performance [] Health checkups are just as important for grinding circuits as for grinding circuit operators. ...
Abstract: In the grinding process automatic control, detection and control of ball mill load is the important content of ball mill automatic control. Can detect the ball mill load accurately is a key to the success or failure of intelligent control of the whole ball. In the grinding sound signal measurements, the presence of the noise makes signal characteristics can not …
In this paper, COMSIM, a new simulator which runs under Excel spreadsheet will be introduced which uses a Population Balance Model (PBM) to simulate ball mills. Plitt and Nageswararao models have been used to describe the performance of hydrocyclones, which by linking to the ball mill model allow for closed-circuit simulations.
Dobby & Starkey method using a timed laboratory SGI Mill for SAG milling. Peter A. Day 2 08:30-10:30 Non-standard particle size distributions, the phantom cyclone and ball mill CF factors, geometallurgy and sampling an orebody. Alex D. 10:30-11:00 Coffee break AM 11:00-12:30 Mill power draw models for ball mills and SAG mills. Alex D. 12:30-13 ...
As each ball weighs ∼ 1.4 g, this corresponds to ball-to-sample weight ratios of 7 and 14, respectively. Such conditions are sufficient …
How cyclones work • All cyclones work by centrifugal force • Two main factors affect cyclone efficiency – velocity particle moves towards the wall or collection area of the cyclone where it is
3.3 Ball Mill Design The ball mill designs also follow the Bond/Rowlings method with comparison with other methods. Again the method of use is the same 3.4 SAG/BM Combined design This is the combined model of the SAG and BM models. The difference is that a provision in the BM model allows for the fact that finished product is in the BM feed.
Molycop Tools© 3.0 is a set of 63 easy-to-use EXCEL spreadsheets designed to help process engineers characterize and evaluate the operating efficiency of any given grinding circuit, following standardized methodologies and widely accepted evaluation criteria.
Method and material The experimental execution conditions of the standard Bond test, together with the specification of the Bond mill are given in Table 1. Table 1. Bond's mill specification and grinding conditions Mill diameter, D m, cm 30.48 Mill Length, L m, cm 30.48 Number of mill rotations in minutes, n, min-1 70 Mill balls weight, M b
The nonchaining spreadsheets can be caught in a circular reference where a step change proceeds around the circular reference from cell to cell without dampening-out. An example would be a closed-circuit ball-mill feed calculation cell that contains the value 100 on the first iteration, 0 on the second, then back to 100 again repeating the cycle.
Figure 4 gives a flow diagram where a ball mill receives new feed pulp, hydrocyclone underflow and sometimes water and produces a pulp. Exponent i and o will designate respectively inlet and
Design Method of Ball Mill by Discrete Element Method collected. The diameter of the gibbsite powder was measured using a Master Sizer 2000 (Sysmex Corpora-tion). Details of the experimental conditions are given in Table 2. Results and Discussion 1. Effects of Fins on Ball Motion in the Mill To predict ball mill grinding behavior using the dis-
Ball mills consist of a hollow cylinder mounted such that it can be rotated on its horizontal longitudinal axis. Commonly, stainless steel ball is used as grinding media in the ball milling method. Stainless steel ball is chosen because it low contamination of the material being processed and contains high density.
Watch this video to learn about Ball Milling MethodTo learn more register at
Stamp mill,Crusher, AG mill, SAG mill, Pebble m ill, Ball mill, Rod mill. A stamp mill ... (150µm). Grinding is usually done by mills. Grinding methods are . widely used in the fields of m ...
The geometry of a mill with conical ends is shown in Figure 8.6. The total volume inside the mill is given by Vm 4 D2 mL 1 2(Lc L) L 1 (Dt/Dm) 3 1 Dt/Dm (8.16) The density of the charge must account for all of the material in the mill including the media which may be steel balls in a ball mill, or large lumps of ore in an
Milling in a planetary ball mill is the most frequently used method to get carbon aerogel powder, where the monolithic aerogel is placed in a container with balls made of, e.g., ceramic or steel [9, 10]. The container of the planetary ball mill mechanically rotates on its axis and powders the material to fine powder through the pressure ...
94 x 0.61" balls. The optimum number of grinding balls is 285. However, the ball diameters vary due to wear. Therefore, the total ball number should be adjusted from time to time to ensure a total mass of 20.125 grams. The grinding jar of the Bond Index Ball Mill measures 12″ x 12″ and has well-rounded corners. Module Rod Mill.
حقوق النشر © 2024.Artom كل الحقوق محفوظة.خريطة الموقع