Lime kiln - ANDRITZ
Producing consistently high-quality burnt lime for slaking requires not only deep knowledge of the calcining process, but also effective energy conservation and emissions control. The lime kiln is a huge consumer of energy in a pulp mill, and a large potential generator of CO 2 emissions. Energy and emissions need to be adequately controlled to ...
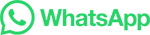