A Review of Methods for Synthesis of Al Nanoparticles ...
The different type of ball milling can be used for synthesis of nanomaterials in which balls impact upon the powder charge [12]. High-energy ball milling is a convenient way to produce nanosized powders. It is the most common method reported in the …
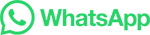