Temperature progression in a mixer ball mill | SpringerLink
12%For example, it was shown that milling in a mixer ball mill (MBM) for 10 min with two milling balls in a 10 ml beaker raised the temperature from 25 to 30 °C, and Colacino and co-workers measured a temperature increase of approximately 14 K after 30 min milling in an MM200 mixer mill [ 6, 11 ].
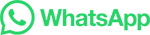