Optimization of mill performance by using
However, the example of liner design and grinding efficiency uses the media charge angle only. Other examples will explore the interaction between the pulp and the media load. Influence of slurry properties and load behaviour in tumbling mills
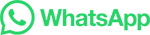