Wet Ball Milling Vs Dry Ball Milling | Orbis Machinery, LLC.
The advantages Wet ball milling has over dry milling are higher energy efficiency, lower magnitude of excess enthalpy, better heat dissipation and absence of dust formation because of the aqueous environment it is being performed. Particle Size Reduction. Milling the powder in the wet or dry state produces different results.
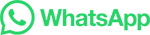