ApplicAtion note Grinding Tools
Choosing the correct grinding tool and accessories will help to ensure con-tamination-free preparation of a great variety of sample materials. result in damage to the grinding tools in a mix-er mill or a planetary ball mill. This is especially crucial for high-energy grinding over long peri-ods. Too much sample in the grinding container
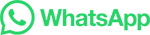