causes and solutions of ball mill noise |mining pedia
Ball mill is a piece of important grinding equipment, which is widely used in mineral processing, building materials, and the chemical industry. It can be used for dry or wet grinding of various ores and grindable materials. However, the noise generated by ball mills in the production process is extremely loud and can easily damage the health of workers who …
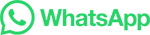