The Effect of Ball Size Diameter on Milling Performance
the other mills, as previously mentioned ball mills have a very low efficiency in terms of utilizing the energy generated towards particle size reduction. The diameter of the balls used in ball mills play a significant role in the improvement and optimization of the efficiency of the mill [4]. The optimum rotation speed of a mill, which is the ...
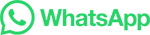