The MVP of Cement Raw Mill Rotary Feeders! - Precision ...
1.3 TECHNICAL FEATURES OF CEMENT PLANT 1. To support friction drive in Kiln, eliminating the use of lubricants. 2. Raw mill does not require water sprinkling, it induces less hot air reducing energy & water Consumption. 3.
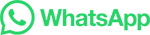