RAW MATERIALS IN CEMENT PRODUCTION
The only common feature in all cement production plants is the difficulty of grinding the source material as the material is hard enough and has high abrasiveness. That is why high quality grinding balls with high hardness over the entire section are used during grinding materials in tube mills in this industry.
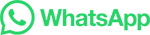