Cement Manufacturing - IFC
in the temperature range of 230–400°C. (For fur-ther details, see United States1991.) Pollution Prevention and Control The priority in the cement industry is to mini-mize the increases in ambient particulate levels by reducing the mass load emitted from the stacks, from fugitive emissions, and from other sources.
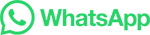