Grinding Media - Union Process
Alumina Balls and Satellites. Union Process is the one source for 90%, 94%, 99.5% and 99.9% alumina media. 90% alumina is available in satellites and rod/cylinders. 94% alumina balls have excellent wear resistance with higher impact strength to save running costs with less contamination. They have great wear rate generally better than 90% or 99 ...
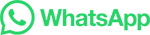