Air Emission Factors for Metals Finishing Operations
ER = overall emission factor reduction efficiency, %. Emissions from Agitation Activities Emissions to the atmosphere are result from turbulence caused by air agitation. US EPA, in AP-42, provides the following algorithm for mixing process tanks with air: (2) E = 1.9 x o/R b
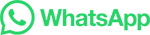