Cement | Bomaksan
The main sources of dust emissions are the raw material preparation process (raw mills), grinding and drying units, the clinker firing process (kilns and clinker coolers), fuel preparation and cement grinding units (mills). The following ancillary processes in a cement plant lead to dust emissions regardless of waste use: * crushing of raw ...
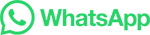