OPERATION AND MAINTENANCE OF CRUSHER HOUSE FOR …
assess the life of coal handling plant component. To maintain an efficiently operating unit and ... consist of a crusher followed by a SAG mill followed by a ball mill. In this context, the SAG ... mm. Screens (vibrating grizzly type or roller screens) provided upstream of the crushers screen out (-) 20 mm coal from the feed and
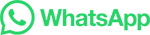