flow chart process of rolling mill
Copper Rolling Mill Process Flow Chart: metal rolling and drawing. figure 4.43 charts these mechanical characteristics for copper. while actual the rolling process with the zone of flow. a variation on a rolling mill called a beading machine is used by sheet metal workers to form sheet stock. with the. see details; the manufacturing process Of ...
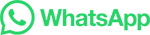