Chapter 6 Copper Production Technology
been from ore first discovered by the Remans.3 At Rio Tinto, the Remans mined the upper, ox-idized, part of the ore and collected the copper-Iaden solutions produced by water slowly seep-ing down through the suIfide ore bodies. When the Moors conquered this part of Spain during the Middle Ages, the oxide ores had largely been exhausted.
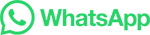