US8172168B2 - Roller grinding mill - Google Patents
A roller grinding mill is provided that includes a grinding plate, grinding rollers, and at least two drives acting upon the grinding plate, and to a method for operating such a roller grinding mill. At least one grinding roller and substantially simultaneously at least one matching drive can be disengaged during operation. Thus only small radial forces are created that effect the radial ...
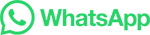