Mill Dirty Air Flow Ch-8.6 - wbpdclewf.in
a balanced 'dirty air' or 'coal flow' distribution amongst the discharge pipes of a mill. The focus needs to be on dirty airflow and coal flow balance measurements. The relative flow distribution between burner pipes is assessed by calculating the deviation of …
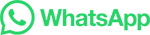