Not another HPGR trade-off study! - ResearchGate
Micro-cracks reduce the Bond ball mill work index of 10-25%, when compared with the product from a tertiary cone crusher [29, 31,32] and that the HPGR is likely to result in weaker coarser ...
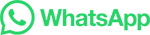
Micro-cracks reduce the Bond ball mill work index of 10-25%, when compared with the product from a tertiary cone crusher [29, 31,32] and that the HPGR is likely to result in weaker coarser ...
lifter packages for AG, SAG, Ball Mills and Scrubbers. Improved throughput, wear life (with indicator layers for easy inspection and monitoring) are the main criteria considered. Pulp Discharge Linings Pulp Lifter Components • Inner and Outer Pulp Lifters • Discharge Cone Liner • Grate Plates • Pan Support Filler Rings • Clamp Rings
bond s work index ball mill inner liners design hot sale low price high quality chrome ore crusher 50 t/h crusher plant flow chart raw mill cement plant ppt grinding mill china coal mobile crusher machine for sale india department of civil engineering concretelab manual
A New Approach to the Calculation of Work Index and the Potential. The work index Wi was defined by F Bond as the specific energy (kWh/ton) required to reduce a particulate material from, tory rod mill and the semi continuous process using the, cylinder, due to centrifugal forces and smash any mineral.
Ball Mill Design/Power Calculation. 08/04/2018 Ball Mill Power Calculation Example #1 A wet grinding ball mill in closed circuit is to be fed 100 TPH of a material with a work index of 15 and a size distribution of 80% passing ¼ inch (6350 microns). The required product size distribution is to be 80% passing 100 mesh (149 microns).
Bond Ball Mill Work Index Da Ase Jktech sehekade Bond mill work index of limestone ball mill,bond ball mill index test jktech a bond ball mill work index may +86 21 33901608 [email protected] Home
Testwork: Bond Rod Mill Work Index. The Bond rod mill work index is not as common as the Bond ball mill work index, and there are two different variations on the mill apparatus. The SAGMILLING models expect a mill with a "wave liner", and is not compatible with mills using "smooth liners". Most laboratories outside of Australia use the wave ...
Minerals rod mills for sale,Wire Rod Mill,sand making machine in ... design of bond rod mill work index - Crusher South Africa . Obtenir le prix. ... Fuller-Traylor Ball Mills are the most robust design in the industry. ... These standardized designs provide ... Obtenir le prix.
Where, WioACTis the Actual Operating Bond Work Index (kWh/t), W is the specific energy input (kWh/t), P80 is the 80% passing size of product (µm), and F80 is the 80% passing size of circuit feed (µm). 2. Calculate the Standard Circuit Bond Work Index (WiSTD) for the material being processed (equation 3). Wtotal
p of ball mill product passing sieve size P 1 produced per mill revolution. The rest of the terms are defined as in Equation (1). The work index obtained following the standard Bond grindability test described above predicts the energy requirement for a 2.44 meter (8ft.) inside liners diameter, prototype ball mill under the following
JK Bond Ball Mill Test Since its introduction in the 1960s, the Bond Ball Mill Work Index (BBMWi) parameter has been extensively used in predicting ball mill power draw. Use of Work Index Along with comminution circuit design the work index parameter is widely used in tracking mill performance. Due to the age and lack of controls for the test,
The Bond Ball Work Index Test determines the resistance of ore to grinding in a ball mill, expressed as a work index kilo Watt-hour per ton (kWh/t). The work index is then used to calculate the specific energy requirements for sizing ball mills or determining their throughput for a target grind. Sample Requirements: 10kg -3.35mm
Mill Type Overview. Three types of mill design are common. The Overflow Discharge mill is best suited for fine grinding to 75 – 106 microns.; The Diaphram or Grate Discharge mill keeps coarse particles within the mill for additional grinding and typically used for grinds to 150 – 250 microns.; The Center-Periphery Discharge mill has feed reporting from both ends and the product …
Successful liner design begins before grinding mills are manufactured: At the new project stage of development, ME Elecmetal will provide total liner project coordination. We work closely with the grinding mill supplier, engineering contractor and mill end user at …
With a Bond Work index-based Phantom Cyclone Approach (1989) *E SSBM for secondary/tertiary crushing and single-stage ball milling (Rowland, 1982) Net power for AG/SAG mills kW (net) = P N * ρ * D 2.5 * L. Legend. P N = power number* ρ = mill charge density (Loveday, 1979) D = diameter (net effective inside shell liners/lifters)
A Ball Mill Critical Speed (actually ball, rod, AG or SAG) is the speed at which the centrifugal forces equal gravitational forces at the mill shell's inside surface and no balls will fall from its position onto the shell. The imagery below helps explain what goes on inside a mill as speed varies. Use our online formula. The mill speed is typically defined as the percent of the …
However, Bond Work Indeces are related to the type of equipment to be used (rod mill, ball mill, SAG uses Drop Ball parameter-Kwhr/m3-, so it is more complex than just specific energy consumption ...
The basic parameters used in ball mill design (power calculations), rod mill or any tumbling mill sizing are; material to be ground, characteristics, Bond Work Index, bulk density, specific density, desired mill tonnage capacity DTPH, operating % solids or pulp density, feed size as F80 and maximum 'chunk size', product size as P80 and maximum and finally the …
A Bond Work index mill ball charge and closing screen product size distributions for grinding crystalline grains Int. J. Miner. Process., 165 ( 2017 ), pp. 8 - 14, 10.1016/j.minpro.2017.05.011
A method of grinding a mineral-containing ore, which includes grinding the mineral-containing ore in a primary milling process and thereafter fine grinding the mineral-containing ore in a secondary ball-mill. A composite grinding medium comprising a mixture of steel balls and pebbles is used in the secondary ball-mill. The pebbles have an average size which is …
Design for Comminution circuits. Bond Ball mill Grindability Grindability Tests The rod mill work Index is also normally distributed with and average and median of 14.8kWh/t It is common to observe difference between the ball and rod mill caused by variation in ore hardness. The test has been mainly used for the design of rod mill or primary ...
Comparison of UCS to Bond Work Indices. FIGURE 8: ROD MILL/BALL MILL WORK INDEX RATIO v. UNCONFINED COMPRESSIVE STRENGTH 100 200 300 400 UCS (MPa) 0 0.5 1 1.5 2 WiRM/WiBM (metric) Siddall et al (1996) identified the ratio of Bond rod mill Work Index and ball mill Work Index as being indicative of an ore's compentency.
Bond's approach consists of determining the ore hardness characteristics, or Work Index (Wi) via standardized laboratory testwork. The full suite of Bond comminution tests provide the Ball Mill Work Index (BWi), the Rod Mill Work Index (RWi), the Crusher Work Index (CWi) and the Abrasion Index (Ai).
The Bond Ball Mill Work Index (BBWi) test is carried out in a standardised ball mill with a pre-defined media and ore charge. The Work Index calculated from the testing can be used in the design and analysis of ball mill circuits The test requires a minimum of 10kg of sample that has been stage-crushed to passing size of <3.35 mm.
First, a Jar Mill grindability test requires a 5 lb. (2 kg) sample and produces a direct measured specific energy (net Hp-hr/t) to grind from the design feed size to the required product size. The second test, a Bond Work Index determination, results in a specific energy value (net Hp-hr/t) from an empirical formula.
We require a minimum of the feed size (F80), product size (P80), Bond Ball Mill Work Index (kWh/mt), feed rate (tons/hr) and Ore Specific Gravity (t/m). However, we would prefer to have more detail so that a proper mill sizing assessment can be completed. Please complete the attached form with as much detail as possible.
An improved method using less mass compared to the Bond Ball Mill Work Index test. The JK Bond Ball Mill (JKBBM) test, is a locked cycle grindability test conducted using a standard laboratory Bond Ball Mill with the same steel ball charge and material feed size ( passing 3.35 mm) as the Bond Ball Mill Work Index test.
Ball mill design requires a Bond work index, BWi, for ball mills at the correct passing size; SAG mill design requires an appropriate SAG test, for example, SPI (Chapter 5 ). Flotation design needs a valid measure of kinetics for each sample, including the maximum attainable recovery and rate constants for each mineral ( Chapter 12 ).
The Bond work index determination according to the standard Bond's test is done on all these samples with compara-tive sieve size of 74, 105 and 150 microns. The Bond Work Index is calculated using the formula (Bond, 1961): (√ √) (1) where: W i – Bond work index (kWh/t); P c – test sieve mesh size (µm);
However, this requires a significant amount of ore samples, a lot of labor and the pilot plants. Fred Bond published an article in 1961, which, described the procedure for testing ores for a Bond Ball Index. This parameter is still one of the most demanded tools in the design, evaluation and optimization of ball grinding plants around the world.
حقوق النشر © 2024.Artom كل الحقوق محفوظة.خريطة الموقع