(PDF) Selection and design of mill liners
Protection of the mill shell and the end walls from the aggressive impacting and abrasive environment inside a mill is well known as the primary purpose of mill liners (Powell et …
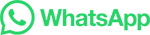
Protection of the mill shell and the end walls from the aggressive impacting and abrasive environment inside a mill is well known as the primary purpose of mill liners (Powell et …
1. Liners protect the outer shell of the mill from wear - liners are renewable. 2. Lifters prevent slipping between the medium and slurry charge in the mill and the mill shell. Slippage will consume energy wastefully but more importantly it will reduce the ab ility of the mill shell to transmit energy to the tumbling charge.
Blind liner - Mill head 5000 80 12000 2,47 3,09 2,8 7467 0,864 -0,005 Shell liner 1st comp. 46000 45 30000 5,11 11,36 2,8 27477 3,180 -0,050 ... Total cost of mill internals of a vertical cement mill Component Weight Price Operating lifetime Specific Price Wear cost Specific wear
Procedure For Replacing Ball Mill Liners And Lifters. Replacement Of Cement Ball Mill Shell Classifying Liners. Learn more. Detail About. cement mill liners « mining equipment. Classification liner for the For the conventional mill using a liner with lifter, You Can Buy Various High Quality Cement Ball Mill Liners Products from. get price
11.6 Portland Cement Manufacturing 11.6.1 Process Description1-7 Portland cement is a fine powder, gray or white in color, that consists of a mixture of hydraulic cement materials comprising primarily calcium silicates, aluminates and aluminoferrites. More than 30 raw materials are known to be used in the manufacture of portland cement, and these
progressive shape evolution of liner surfaces is developed and validated by the wear profiles of the shell liner in the first chamber of a 5.8 m diameter cement mill monitored during a decade by Magotteaux International S.A. . The energy dissipated by tangential damping defined by the
Mill linings, Rubber Engineering, Salt Lake City, UT 84126, United States of America . ABSTRACT . Dramatic shortcomings of mill liner designs, especially of large SAG mills, - such as rapid failure and even mill shell damage arising from impacting of the charge directly on the liner, and unsuitable
In an effort to reduce downtime, increase productivity and increase the milling efficiency of their SAG mill, a leading gold and copper mine in South America conducted side-by-side tests of FL's high-performance, lightweight PulpMax™ Composite Shell Mill Liners and liners from another supplier. It also gave the mine the opportunity to evaluate both …
Cement – Vertical mill parts. GRINDING ROLLS FOR VERTICAL MILLS IN THE CEMENT INDUSTRY. The operating parameters of vertical mills are seldom altered once optimum productivity is established. But efficiency improvements – and therefore cost savings – can still be achieved with developments in metallurgy of the grinding element.
Advantages of Shell Mill Liners: Optimum lifting action of the balls. Optimum expansion of the ball charge. Minimize the dead zone of the ball charge. Significant reduction of the wear rates of the ball and the liners. Minimum operating cost due to longer lifetime and no breakage of the liner plates. Note : Depending upon the various ...
Cement Mill Operation China Pdf. This page is provide professional pdf vertical grinding mill for. The objective is to achieve a more efficient operation and increase the production rate as well as improve the run factor. It is lined with classifying-type mill shell liners and provided with finer ball charge.
Design of cement mill liners There are several types of cement mill liners: feed-end-liners, lifting-liners, classifying liners.They all have some features in common. Magotteaux determines the optimum design and alloy for cement mill liners to give the best mill protection. This is done according to a variety of factors such as shell liner type, rotation speed, maximum ball …
Rod mill liners are subjected to severe impact. Premature breakage and scrap loss are reduced by correct selection of liners for the specific grinding duty. Additional benefit results from use of a backing material, such as rubber between the liners and the mill shell. Single wave liners are recommended for larger size balls (50mm/2.5″ and ...
Through Welding Alloys technology, cement plants across the globe have benefited from reduced VRM grinding component wear, longer lasting mill shell liners, roller hub guards and various other products and solutions to enable them to increase productivity, optimise mill efficiencies and simultaneously reduce costs. ifecycle
• The selected Shell Provisional will be identified through a size and a two letter code (e.g. 50 HH). There are different inner diameter Implant sizes available for each Shell size. The Provisional Liner will be identified by letter code matching the Shell diameter and desired inner diameter (e.g. 32 HH).
The rubber liners inside the mill are critical components for mill shell protection and ore grinding. The replacement and inspection of mill liners are major factors ... study for mill liners", Journal of Quality in Maintenance Engineering (Accepted) Paper IV Dandotiya, R. and Lundberg, J. (2011), "Combined replacement and life improvement ...
for a cement plant in Central Asia KORFEZ ENG. has received a follow-up order in April 2015 to design and manufacture complete mill internals for a 3.8 m diameter two-compartment cement mill. The order includes inlet head liners, all mill diaphragm plates as well as the mill shell lining for both grinding compartments.
— shell replacement with shimming Optimization systems — Remote process monitoring — Theoretical and on-site training — Mechanical revamping for kilns and mills (tyres, rollers, gears, liners, grids, sho e-bearings, lubrication units, driving units...) — Equipment and plant upgrades (Kiln seals replacement, supporting
Cement Ball Mill Operation Pdf - manufacturer, factory, supplier from China. (Total 24 Products for Cement Ball Mill Operation Pdf) Rubber Liner Ball Mill. Brand: HP Plate. Packaging: Steel Frame or Wood Case. Supply Ability: 500 tons per year. Min. Order: 50 Kilogram.
When calculating the thickness of the mill shell, it should be considered that the bolt holes for the mill liners reduce the strength of the shell by about 11%. 4.2 Shell Liners: Clinker grinding is performed in two different stages: in the first stage where material must be crushed, sufficient impacts are required to reduce coarser particles ...
Where grinding efficiency meets mill shell protection. The MVL TM, Magotteaux Variable Lift, liner range covers a large bandwith of shell liners for coarse, medium and fine grinding. The liners are energy efficient and ensure a very low grinding media consumption. Your key benefits: Optimum compromise between lifetime and grinding efficiency.
Cement – Tube mill internals – Shell liners LINERS MADE TO LAST LONGER IN CEMENT MANUFACTURING The Group Industries manufactures Inlet discharge Head First Chamber and Second Chamber Liners to provide optimum productivity and power consumption for all types of Tube Mill used in the Cement industry Tube Mill Internals Shell Liners for Cement ...
The quality of the shell lining is decisive for the production potential of the grinding processes, because the dynamics of the grinding media movement inside the mill is mainly defined by the shape of the mill shell lining. For this reason, Christian Pfeiffer optimally designed shell linings which, thanks to different fastening systems (bolted ...
MARCY 8 x 6 Ball Mill, Shell, Gear and Liners, Parts Unit. Angle of nip.pdf. ... Ball Mill Maintainance. Process analysis and energy efficiency improvement on Portland limestone cement grinding circuit.pdf. Frequency Ranges. Ball Mill Maintenance and Installation Manual Procedure Guide. Ball Mill Grinding Media Max Ball Size Calculation.
It is widely used in clinker grinding production of cement plant and slag grinding plant. CHAENG can provide various types of vertical cement mills with productivity of 50-250t/h. The biggest advantage of CHAENG is to have a large casting base and large machining workshops, which greatly shortens the delivery cycle of cement vertical mill.
CEMENT ROTARY KILN Questions & Answers Question-1: What is the maximum continuous shell temperature a kiln stands without permanent damage to the shell? Answer-1: The maximum recommended kiln shell temperature varies by plant, by country and by kiln manufacturer, despite the fact that most kiln shells are made of low alloy carbon steel.
The liner of cement dry-type ball mill can be divided into ceramic, granite, rubber, high manganese, magnetic liner and other materials. The function of liner is mainly to protect the cylinder from the direct impact of materials and steel balls and extend the service life. At the same time, the liner plate can also adjust the running track of ...
Liners for grinding mills having alternating bars of alloy steel and strips of an elastomer, such as rubber, bonded together and to a backing plate which is sufficiently flexible that the liner may be manufactured flat, but drawn against an arcuate portion of the cylindrical side wall of the mill by attaching bolts. Converging slots formed in the center bar of the liner are engaged by bolt ...
for mill liner change outs, including: • Extruded Filler Pieces • Extruded Corner Segments • Mill liner rubber backing, 6, 9 and 12mm thick Trelleborg supply all fastening components required for mill liner change outs, including: • T Bolts & Clamp Blocks • Cup Washers • Integral Sealing Washers Mill Lining Auxiliary Equipment
cement industry where mill sizes typically range between 15ft and 18ft. The aim was to offer a low-cost, efficient and easy to assemble GMD that embodied 40 years of mill drive experience in the mining industry. While larger mill drives come in four or even five segments that need time-consuming interconnection on site, the
حقوق النشر © 2024.Artom كل الحقوق محفوظة.خريطة الموقع