End Mill Size Standards (American) – Automated Production ...
End Mill Size Standards (American) December 20, 2016 January 17, 2017 apmmfg. This chart references all the standard end mill tool sizes in American measurements. Also available in PDF format to download for future reference. Fractional Decimal Fractional Decimal; 1/64.0156: 5/16.3125: 1/32.0313: 21/64.3281: 3/64.0469: 11/32.3438: 1/16.0625: 23 ...
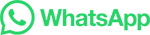