CEMENT PRODUCTION AND QUALITY CONTROL A. Cement ...
4 Raw material Grinding and Transportation In this unit, the proportioned raw materials are being ground to the size of (10% residual on 90 μm sieve) by closed circuit ball mill in line 1 and Vertical Roller Mill (VRM) in Line 2. While grinding; the raw materials are being dried from 4% moisture
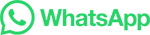