Effects of Multi-stage Grinding Process and Grinding ...
Grinding process and fineness have been found as significant factors influencing the flotation desulfurization performance of high-sulfurous iron ore. Moreover, the separation tests of multi-stage grinding as well as direct one-stage fine grinding were conducted.
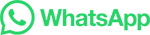