(PDF) An investigation of performance characteristics and ...
In a coal-fired power plant, one of the main equipment is the coal mill, whose effectiveness influences mainly the whole power plant performance (Shah, Vuthaluru, and Vuthaluru 2009 ).
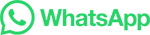
In a coal-fired power plant, one of the main equipment is the coal mill, whose effectiveness influences mainly the whole power plant performance (Shah, Vuthaluru, and Vuthaluru 2009 ).
Coal Grinding. To achieve good combustion and satisfactory flame formation, coal needs to be dried and ground to a proper degree of dryness and fineness. Drying of moisture in coal is achieved normally by ducting part of the kiln exhaust gas through the mill with inlet temperatures of up to 300°C. Inert kiln exhaust gases with oxygen content ...
FIGURE 7-2. Coal production and consumption in the U.S. in the past 150 years. [Source: Energy Information Administration.] Coal Formation As described in the general discussion of the carbon cycle (Chapter 6), coal was formed from prehistoric plants, in marshy environments, some tens or hundreds of millions of years ago.
Pulverizers 101: Part I. Every coal pulverizer is designed with a particular fuel grinding capacity or throughput at a certain Hardgrove grindability index (HGI), based on a …
The analysis of individual mill design and operation is complex; so, for simplicity we will consider a typical mill layout for one mill type only. As VSMs have come to represent the bulk of the power station mill fleet, the explanation of mill operations will be based on this mill type. ... In addition, fossil plant requires either coal mills ...
1927 First Loesche coal mill delivered for the Klingenberg power station in Berlin. 1953 500th coal mill plant sold worldwide. 1961 Introduction of hydraulic spring assembly system. 1965 Construction of first pressure mill (LM 12.2 D). 1980 Delivery of first modular coal mill (LM 26.3 D). 1985 Delivery of first self-inerting coal grinding plant (LM 21.2 D) for the steel industry …
Even in routine mill shutdowns, there is a danger that any residual coal left within the mill will oxidise, and may explode as the mill is restarted. The Millwatch system is installed near the classifier and can detect the CO emitted from any hot inclusions within the residual coal. With many baseload plants now
In mining operations, the layout of crushing plants and ancillary equipment and structures is a crucial factor in meeting production requirements while keeping capital and operational costs to a minimum. This paper addresses the critical design parameters as well as the consideration of ore characteristics, geographical location, climatic conditions, expected …
We specialize in coal mills: in particular performance upgrades to meet the increasing demands on the world's power generation i ... ndustry. We provide a comprehensive service for major milling plant modifications, including investigations, feasibility studies, design, manufacturing, installation and commissioning.
The crushed coal is then transported to the store yard. Coal is transported to bowl mills by coal feeders. 3. Bowl Mill. The coal is pulverized in the bowl mill, where it is grounded to a powder form. The mill consists of a round metallic table on which coal particles fall. This table is rotated with the help of a motor.
Mps Coal Mill Lift And Swing System. POWER SERVICE – APComPower, Inc.: Maximum lift and drag … original classifier for the MPS mill. It … the mill can process this coal with few operational problems. Click & Chat Now. CEMENT. for grinding cement raw materials and coal.
Ball mills (Fig 1.1) are coming in cement plant areas of raw grinding, coal grinding and cement grinding which in turn as raw mill, coal mill and cement mill. Ball mills are horizontal tube mills having single or two compartments for grinding, Balls as grinding media and driven by …
The Plant Load Factor (PLF) of state-sector thermal power plants in India in 2006-07 was on an average 70.84 percent compared with 89.4 percent for central-sector NTPC power plants and 86.35 percent for private-sector power plants. Among the state-sector power plants also, there is a wide performance range with more than 90 percent PLF for some
So if the process layout allows, the coal mill should be set near the kiln tail as far as possible. We also need to strictly control the temperature of the gas-powder mixture at the coal mill exit as reducing the temperature not only ensures the safe and stable operation of the grinding system but also reduces the coking of the burner.
a power plant including the coal handling facilities, pulverising mills, boiler, air heater, ESP, ash disposal as well as stack emissions. Figure 1 is a diagram of a typical pulverised coal combustion power station. Table 1 is the stages that require monitoring in a coal-fired power generating plants (as shown in Figure1).
Mill Rejects from coal mill will drop into the Pyrite Hopper through the grid. Oversize material will be retained on the grid. A pneumatic cylinder operated Plate Valve on oversize material discharge chute will be provided, which will be operated automatically in case of accumulation of oversized rejects.
Coal mill employed at coal fired power plant. In coal fired energy plant, coal mill is employed to grind, pulverize and dry coal ahead of the coal is transmitted the boiler. The coal is feed into the coal mill by way of a inlet pipe so that the roller coal mill such as Raymond mill and vertical mill can pulverize the coal into particles.
which resulted in a significant improvement in plant efficiency. A 's-eye view of Matsuura Power Station is shown in Fig. 1. The Matsuura No. 2 Unit, whose steam parameters are 24.1 MPa/593°C/593°C, achieved the highest live Design and Operating Experience of the Latest 1,000-MW Coal-Fired Boiler Fig. 1—'s-Eye View of the Matsuura
Indian coal power plants). Out of the current 197 GW installed coal capacity in the country, about 187 GW capacity has to meet the NO x emission norm of either 600 mg/Nm 3 or 300 mg/Nm. Only 10 GW capacity, or 5 per cent of the total, has to meet the 100 mg/Nm3 standard (see Figure 1: Age-capacity profile of Indian coal power plants).
Coal Mill - an overview | ScienceDirect Topics
Vertical coal grinding mill integrates crushing, drying, grinding, powder selection and conveying.; It has simple system and compact structure. Vertical coal mill covers an floor area about 50% of the coal ball mill with the same specification.; Coal vertical mills can work in open-air environments, greatly reducing the cost of investment. The design of the vertical coal mill …
coal handling power plant mill machine layout. coal handling power plant mill machine layout ball mill machinery manufacturer in tamilnadu Matla CoalFired Power Station Eskom MATLA a Sotho word meaning strength or power has taken on a new meaning in the Eastern Transvaal now Mpumalanga T he coalfired power station bearing.
2.Coal pulverizer/mill system One of the critical power plant components that is relied upon to convert the energy stored in coal into electricity is the coal pulverizer or mill. The coal flow is controlled by the feeder, allowing coal to flow into the pulverizer mill. The pulverized coal and air mixture is then transport to the boiler burner ...
Construction Details of Steam Power Plant: The layout of the steam power plant consists of the following parts. ... Utilization in industries like sugar mills, chemical industries, etc. ... After burning of the coal, it is transported to ash handling plant and finally to the ash storage.
A higher Hardgrove index indicates the coal is easier to grind. 50 HGI normally is taken for calculating the base capacity of the mill. When coal with HGI higher than 50 is fed to the pulverizer, the output will be higher than base capacity, and below 50 HGI, the output will be lower. The total moisture in coal has a high effect on mill output.
emissions in coal-fired power plants, Riley Power Inc. (RPI), a Babcock Power Inc. (BPI) company has been actively developing mill system technology to achieve better coal fineness, increased capacity, greater reliability, and longer wear life. The effort has improved the design of low, medium, and high
Coal mill is also called coal pulverizer or coal grinder. It is a mechanical device used to grind raw coal into pulverized coal powders. The most used coal mills in cement plants are air-swept ball mill and vertical roller mill.. At present, most cement plants use coal as the main fuel in the clinker production process.
Distribution of the coal flow in the mill-duct system of the As Pontes Power Plant using CFD modeling J.L Ferrin a'*, L Saavedra b a Departamento de Matematica Aplicada, Universidad Santiago Compostela, 15782 Spain b E.T.S. Ingenieros Aeronauticos, PL Cardenal Cisneros 3, Universidad Politecnica de Madrid, 28040 Spain ABSTRACT The efficiency of a Power Plant …
The main function of the Primary air fan or PA fan is to carry the pulverized coal to the furnace as fuel for combustion. This process is used to create the steam that is the primary process in the thermal power plant. In power plants, the PA fans supply air for conveying of the pulverized coal from coal mills to the furnace area.
The Kaymoor Mine and processing plant in West ia employed more than 800 workers in the early 1900's, with operations coming to an end in the early 1960's. The small local town site once served by the Chesapeake and Ohio Railroad ultimately became one of many coal mile ghost towns.
حقوق النشر © 2024.Artom كل الحقوق محفوظة.خريطة الموقع