A Innovative Solution to the Problem of Mill Rejects in ...
The eros ive wear caused by pulverized coal can significantly reduce the life of milling plant components and coal pipes. The ash erosive wear can lead to …
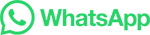
The eros ive wear caused by pulverized coal can significantly reduce the life of milling plant components and coal pipes. The ash erosive wear can lead to …
As discussed previously, the primary types of solid wastes generated by the mining industry are overburden and waste rock from surface mining, waste rock from underground mining, bulk tailings from metal-ore and non-metal mineral beneficiation and milling processes and refuse from coal preparation-plant processes.
The Williams Lake plant also holds the distinction of having the largest single boiler (60 MW) and the lowest heat rate (11,700 Btu/kWh) of any biomass-fired power plant. Biomass-cofired coal plants can achieve slightly lower heat rates, as exemplified by Greenidge Station (11,000 Btu/kWh on the biomass portion of the fuel, compared to 9818
At one of these plants, high-chlorine coal is about 10% to 20% of the total burned, alternating with other ILB coal, with the coal testing at 0.25% to 0.27% chlorine.
Coal-fired boilers are mainly operated at either subcritical or supercritical conditions. From a thermo-physics perspective, two phase mixtures of water and steam are replaced by a single supercritical fluid when the boiler pressure increases above the critical pressure of 22.12 MPa and the corresponding saturation temperature of 374 °C (Shen and Cheng, 2004).
As coal plants produce power, they also produce toxic pollutants that can cause a range of health problems. Those include. Lung conditions like bronchitis, emphysema, asthma, and chronic obstructive pulmonary disease ; Heart conditions like heart attacks, arrhythmias, and congestive heart failure; Brain and nervous system conditions like ...
Aug 10, 2004 ... plant. There are, however, a number of problems for the smooth running of ... from raw and cement mills, 1.5 per cent from coal mills and 0.9 per cent from packing plant. ... wastes such as flyash from thermal power stations, blast furnace slag from iron .... Use of ESPs is more common in cases where internal.
Crushing Plant Design and Layout Considerations Ken Boyd, Manager, Material Handling, AMEC Mining & Metals, Vancouver, BC ABSTRACT In mining operations, the layout of crushing plants and ancillary equipment and structures is a crucial factor in meeting production requirements while keeping capital and operational costs to a minimum.
The answer to the closing of Comanche 3 has to address all those issues, Schonhaut said. The proposed fate of the power plant, a state-of-the-art coal-fired unit that went online in 2010, is laid out in the electric resource plan, or ERP, and clean energy plan submitted to the PUC by Xcel's Colorado subsidiary, Public Service Company of Colorado.
troubleshooting on the coal milling plant. Free chat online coal mill problems in power plant troubleshooting on the coal milling plant coal mill in power plant problems Coal pulverizermill system One of the critical power plant the mill classifier exhauster and transport pipe is a recognized problem. Pulverizers 101 Part I
The powdered coal from the coal mills is carried to the boiler in coal pipes by high pressure hot air.The pulverized coal air mixture is burnt in the boiler in the combustion zone. Generally in modern boilers tangential firing system is used i.e. the coal nozzles/ guns form tangent to a circle. The temperature in fire ball is of the order of 1300 deg.C.
Coal Grinding. To achieve good combustion and satisfactory flame formation, coal needs to be dried and ground to a proper degree of dryness and fineness. Drying of moisture in coal is achieved normally by ducting part of the kiln exhaust gas through the mill with inlet temperatures of up to 300°C. Inert kiln exhaust gases with oxygen content ...
Failure Of Coal Mill Worldcrushers. Sep 17 2013 a root cause failure analysis of coal mill vertical shaft used in thermal power plant has been carried out the failed parts of the shaft showed the signature of reasons for trunnion shaft failure of coal mill p703 in new. How Rootcause Analysis Solved A Vertical Turbine
There are mainly four units which must be installed in any power plant are: 1. Feed water and steam flow circuit 2. Coal and ash circuit 3. Air and gas circuit 4. Cooling water circuit. In above system Coal & ash circuit is most important role into the power plant. On basis of these coal & ash handling system is generated for the proper operation.
1.Problems existing in the coal flame detection device . About combustion of inferior coal in the boiler, coal flame detection device signals appear unstable, frequent fluctuation phenomenon, cause the oil system of interlocking input steady combustion, coal mill tripping, RB action, such as unusual, especially in low load operation stage, the coal mill run …
Direct firing coal mill plant is what is installed in most power generation facilities. The coal mill is operated as an air-swept mill and "blows" directly into the combustion zone of the steam boiler, via a pipeline connection. In case of an explosion, normally as consequence of ignition within the mill chamber, there will be
In a coal based thermal power plant, huge amount of ash is generated which has to be disposed off continuously. Typically for a 2x500 MW plant based on Indian coal, the amount of ash generated is around 300 to 400 TPH depending on gross calorific value and ash content of …
Large coal pulverizers have been identified by EEI surveys as one of the main systems responsible for lost steam generation capacity of large coal fired utility boilers. This report contains the results of a 16 month study to examine the problem of pulverizer outages and to identify root cause failure modes for the major mill types currently in ...
• Manage site/plant access for resources, vehicles, equipment, and tools. • Manage indirect hire, contractor, subcontractor, and service personnel at the site/plant. An effective method is developed for shut down management of coal handling plant of thermal power stations. 3. Maintenance Shutdown Management: -
This is a problem that we hope to tackle in one of the coal plants in the near future. However, for our present studies it has been shown that if stone entry to the mill could be prevented or minimised significantly, lowering ball top-up size to 30 mm would enhance mill performance significantly.
The problems faced in coal stacks and factors affecting the spontaneous combustion of coal like coalification degree, petrographic composition, moisture content, mineral content, particle size, pyrite content are discussed independently. 1. Introduction Like gas and liquid fuel, coal is a material which can be stored in large quantities
To summarize the coal mill controls, they may be divided basically into two major categories:. 1. To control the quality of coal being sent to the burners located on the furnace walls. The word quality here means the temperature and fineness of the PF. The set temperature values are dependent on the percentage of volatile matter that exists in the main fuel.
The coal pulverizers are the heart of a pulverized coal–fueled boiler. About 75% of the opportunities for improvements in tuning are with …
The Chinese government has ordered the country's coal mines to "produce as much coal as possible" as it tries to increase production as winter approaches, and ease an ongoing energy crunch.
Each year hundreds of coal miners lose their lives or are seriously injured. Major mine hazards include roof falls, rock bursts, and fires and explosions. The latter result when flammable gases (such as methane) trapped in the coal are released …
as on-site fuel. Coal has a wide range of moisture (2-40%), sulfur (0.2-8%), and ash content (5-40%). These can affect the value of the coal as a fuel and cause environmental problems in its use. The depth, thickness, and configuration of the coal seams determine the mode of extraction. Shallow, flat coal deposits are mined
The dirty business of apartheid-era dinosaurs: Inside an Eskom coal-fired power plant. People near the Komati Power Station in Mpumalanga search for coal on 8 November 2021. The power station is ...
Coal pulverizer downtime can be a major factor in reducing overall plant availability and reliability. Recommended Filtration Upgrade to Achieve Total Cleanliness Control (See diagrams on back page) The majority of pulverized coal particles are in the 4-30µm range, with 70% of these particles smaller than 10µm.
include such purely in-plant problems as coal dust incident to the grinding and blending of coal, and steam and dust at the coke wharf. Also omitted from the discussion are the fuel-burning processes for the generation of steam, e.g., the burning of the coke breeze
re Coal mill bag filter DP high & chocking problem. 2- If u replace bags after 3 years, now do it after 1.4 years. 3- check ur pressure control diaphragms and pressure regulator diapghrams, if any of them is damage replace it. 4- check leackage in air tube for controller. 6- check that the high pressure pipe before and after pressure regulator ...
حقوق النشر © 2024.Artom كل الحقوق محفوظة.خريطة الموقع