Optimization of Feed Rate in Cement Grinding Mill Using ...
Approximately 95% of the feed to the cement grinding circuit are clinker and the rest of the feed are additives which includes grinding aids. The sequence of operation takes place in Cement grinding mill is as shown in figure 1. Fig. 1: Process in Cement Grinding Mill Raw materials like clinker, gypsum and fly ash are
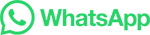