ISO 26423:2009(en), Fine ceramics (advanced ceramics ...
This International Standard specifies a method for the determination of the thickness of ceramic coatings by a crater-grinding method, which includes the grinding of a spherical cavity and subsequent microscopic examination of the crater.
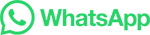