The effect of grinding media J performance on milling and ...
were used in the grinding process to generate a particle size reduction of the calcium carbonate (CaCO3). To determine the optimum milling parameters the collected test data were used to calculate and evaluate specific energy as well as stress intensity under different milling conditions. Keywords: Grinding, mill media, high energy mills ...
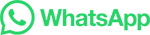