reasons for ball mill bearings failure
reasons for ball mill bearings failure Pulverizing Ball Mill Failures - Machinery Lubrication ... the root causes of failure, as is the case with the ball mill pulverizers, which had ... In the other 65% of the failures, the gears were turned and the bearings... Read more Locked charge starts and your grinding mill - Outotec
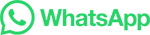