Grinding Machining Process : Complete Notes - mech4study
A grinding machine or grinder is an industrial power tool that uses an abrasive wheel for cutting or removing the m aterial. It is a process of metal cutting by using a rotating abrasive whee l from the surface of the workpiece. Generally, the grinding is finishing operation to show the high surface quality, accuracy of the shape and dimension.
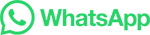