Calculating Ball Mill Throughput
Ball Mill Size And Production Throughput Protable Plant. ball mill size and production throughput-related information, including: Quotes,Price,Manufacturers,Parts : ball mill throughput capacity mineral processing system ...
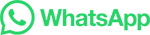